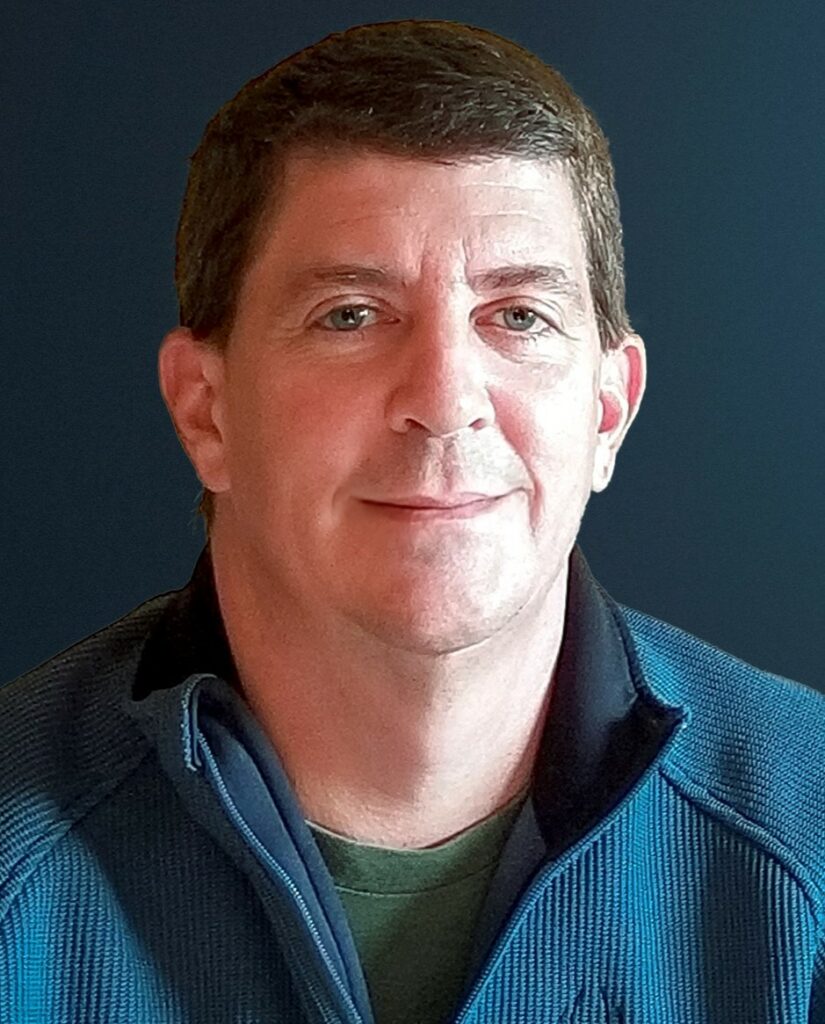
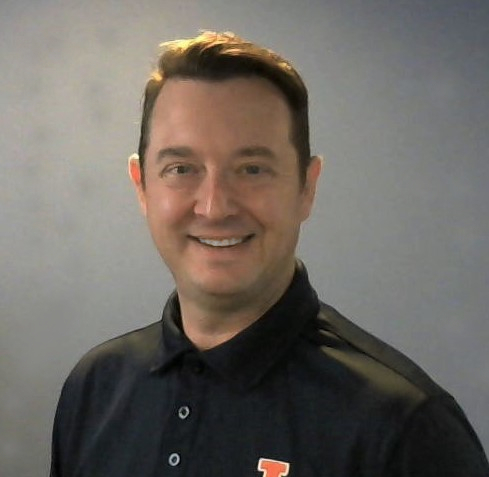
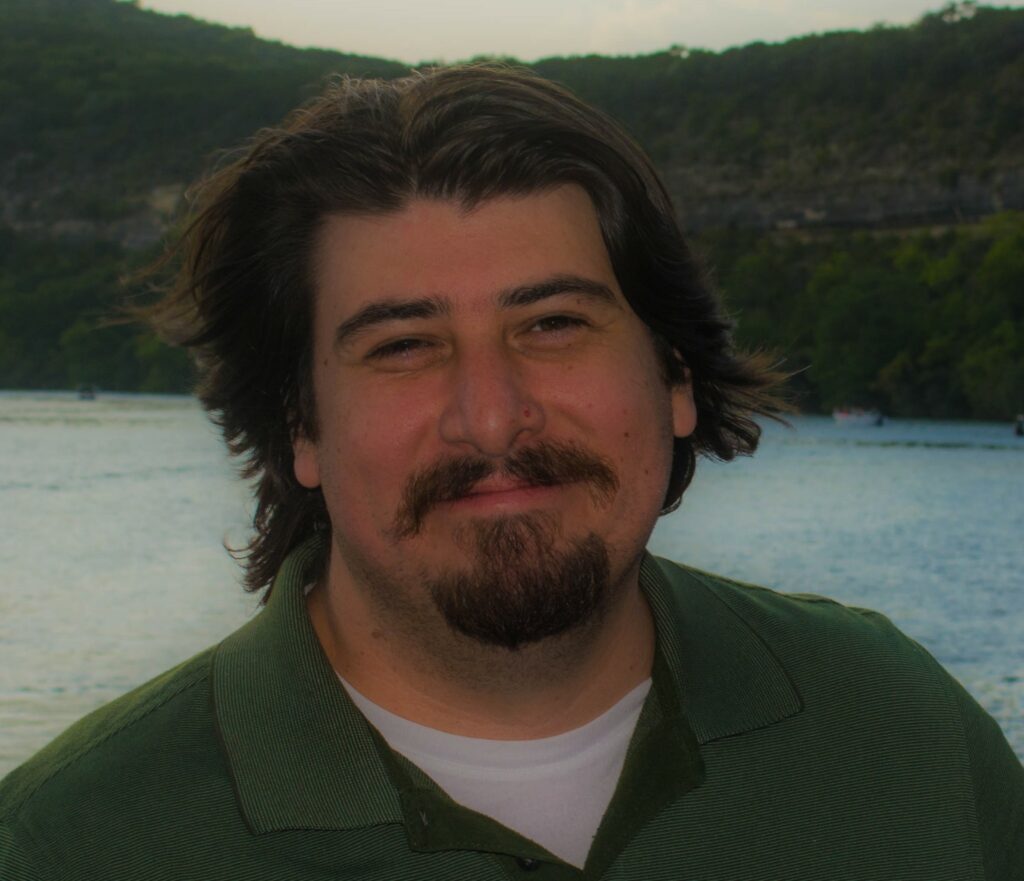
By Cody P. Bann, Nick Becker, and Scott Dappen
As experienced system integrators (SIs) know, an election year brings uncertainty to businesses as they brace for the possibility of policy changes that might affect them negatively.
This uncertainty may cause companies to delay investments and reduce inventories and also create additional risk and disruptions to supply chains.
In addition to the election, the global business environment is becoming increasingly volatile due to systemic macroeconomic and geopolitical changes.
Marsh, a business of Marsh McLennan, recently released its 2024 Global Risks Report, which outlines the major trends in the current global political and economic landscape that will impact multinationals in the year ahead.
The report highlights that, in the coming year, businesses will need to strengthen their ability to identify, prepare for and mitigate difficult-to-predict challenges.
Despite continued volatility and uncertainty, there are substantial global growth opportunities that organizations may benefit from, if these risks are managed effectively.[1]
Workforce Challenges
The U.S. manufacturing industry has emerged from the pandemic on a strong growth trajectory, which is expected over the next 10 years as companies work to meet evolving customer demands, de-risk their supply chains, and leverage government incentives and policies.
Despite substantial growth in the sector, U.S. manufacturing faces a skills gap and tight labor market.[2] According to a Deloitte and Manufacturing Institute study, companies need millions of workers in production and tech roles — as many as 3.8 million additional employees could be needed in manufacturing between 2024 and 2033.[3]
Additional investment in technology could be one answer to help manufacturers overcome these challenges.
Manufacturers Can’t Afford Not to Upgrade Technology
Significant labor and skills gap issues, lingering supply chain challenges and the uncertainty that comes during an election year can be daunting.
However, evaluating the strategic plan and shifting it with the business environment is critical to meeting goals.
Two key questions leadership should ask: Did we keep up with technology? Did we invest in the right equipment?
Falling behind on technology trends can have disastrous consequences, from losing a competitive edge to not meeting customer expectations. The impact that changing technology has on businesses is undeniable and a responsible investment – and perhaps especially because of the current challenges – in technology can go a long way to meeting strategic long-term goals.
New technologies can help companies streamline their processes, improve efficiency and reduce costs. Technology can also help companies stay ahead of their competitors by providing the needed tools to innovate and adapt to changing market conditions.
In The CFO Survey, a collaboration of Duke University’s Fuqua School of Business and the Federal Reserve Banks of Richmond and Atlanta, more than half of respondent firms report implementing software, equipment and/or other technology to automate tasks previously completed by employees,[4] which is important given the widely reported worker shortage and skills gap.
The majority of manufacturers agree on the importance of smart factories and upgraded technology. In fact, in the United States, 86% of manufacturers believe that, by 2025, smart factories will be driving the competition in the industry.[5]
In spite of this, they’re still wary to make commitments right now. As SIs, it’s important to acknowledge the challenges your customers face, but also help them understand the ramifications of not investing in new technology; while the initial outlay may be expensive, not upgrading can be even more costly.
Reiterating the tremendous benefits of upgraded technology will also help drive home the message of increased efficiencies, improved quality control and a better working environment with a more modern facility helps retain younger workers.
A modernized plant also allows companies to tap into new business models, including customization and on-demand manufacturing.
Automated Technology Addresses Challenges
The widespread adoption of robotics is revolutionizing manufacturing as tasks are increasingly automated that were traditionally performed by humans, resulting in gains in efficiency, reduced errors and increased productivity and accuracy.
One example of robotics includes machine tending systems that are designed to reliably and accurately load and unload product from manufacturing machines 24/7 to dramatically improve the quality and consistency of the finished product. Automating rote tasks frees up plant employees for higher-value work, while also addressing the labor shortage challenges.
Robotic palletizing systems are another way to help manufacturers increase production speed and accuracy. Specifically, palletizing is the action of placing products on a pallet for shipment or storage in logistics supply chains.
An automated palletizing process can handle large volumes of products without stopping, outperforming manual processes, resulting in faster production cycles, reduced lead times and increased overall output.
As businesses strive to stay competitive and meet market demands and challenges, the standardized vs. customized robotics cells decision is pivotal. Standardized robotics cells are pre-engineered systems designed to address a wide range of manufacturing needs and come with predefined configurations, components and software, offering a plug-and-play approach to automation.[6]
Customized robotics cells are tailored to meet specific manufacturing requirements and are designed from the ground up, taking into account the unique needs and challenges of a particular manufacturing process. Customization also allows for greater adaptability, ensuring that the cell can evolve with the changing needs of the business.[7]
Technology Reduces Unplanned Downtime
Equipment failure is the most common cause of downtime.
According to analyst firm Aberdeen Research, downtime costs manufacturing facilities an astounding $260,000 per hour.[8]
A Deloitte industry report cited recent studies that show unplanned downtime costs industrial manufacturers an estimated $50 billion annually.
One strategy to reduce unplanned downtime is with remote alarm notification software, which allows fewer people to monitor many more assets using devices that people already have, such as smartphones and tablets. Uninterrupted remote availability is essential to ensuring systems can be continuously monitored, even without staff onsite or with fewer people working at the facility.
Remote monitoring of critical plant systems has been extended beyond email, texts and phone calls to include apps that feature time-saving tools like real-time alarm acknowledgements, team chats to troubleshoot and resolve plant problems, and detailed reporting for preventing future incidents.
Not only does this mean fewer emergency shutdowns, but also fewer resources spent on overtime and maintenance.
A mobile alarm notification app is software that seamlessly integrates with the SCADA or HMI software of an industrial operation, allowing an employee to monitor, receive and acknowledge plant and machine alarms on their smartphones or tablet, freeing them up to work throughout the facility or a remote location.
Hardware and software are available that can constantly monitor equipment and, by applying machine learning to historical data, warn when a breakdown or other problem is imminent.
Bolstered by wireless technology and IIoT, these customizable systems have the potential to bring predictive maintenance to a new level. Through the installation of remote alarm notification software, manufacturers can move from reactive to a more controlled, prescriptive maintenance approach.
Unique Role
SIs play an important role as honest brokers in the process of helping clients navigate uncertain times by listening to their challenges and recommending solutions. The unique expertise brought by a skilled controls system integrator provides an invaluable link between operations teams and IT vendors who offer solutions for operations – like remote alarm notification software – and clients.
Cody P. Bann is director of engineering at Austin, TX-based SmartSights and can be reached at cody.bann@smartsights.com. SmartSights (formerly WIN-911 and SyTech) is a global leader in data-driven analytics, reports and notifications, serving the industrial sector.
Nick Becker is vice president of operations and Scott Dappen is vice president of engineered solutions at Normal, IL-based SCADAware. They can be reached at becker@scadaware.com and dappen@scadaware.comrespectively.
SCADAware is a systems integration and robotics firm that anticipates and provides solutions for the automation needs of clients in many industries, including manufacturing, agriculture, and water/wastewater.
This content is sponsored by Smartsights.
[1] https://www.marsh.com/en/about/media/shifting-macroeconomic-and-geopolitical-structures-undermining-business-confidence-in-2024.html (accessed April 17, 2024)
[2] https://www2.deloitte.com/us/en/pages/about-deloitte/articles/press-releases/us-manufacturing-could-need-new-employees-by-2033.html (accessed April 17, 2024).
[3] Ibid
[4] https://www.fuqua.duke.edu/duke-fuqua-insights/what-landing-cfos%E2%80%99-economic-outlook-improves-first-quarter-2024 (accessed April 17, 2024).
[5] https://www.globaltrademag.com/upgrading-your-manufacturing-5-point-guide-to-a-smart-factory-system/(accessed April 18, 2024)
[6] https://diy-robotics.com/standardized-vs-customized-robotics-cells-making-the-right-choice-for-your-manufacturing-business/ (accessed April 28, 2024)
[7] Ibid
[8] “The Actual Cost of Downtime in the Manufacturing Industry,” November 14, 2018, IIOT World.