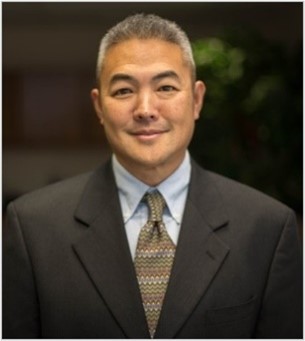
The vital role trusted partners play in this important journey.
By Keith Mandachit, PE, and Barbara Padgett
A million tablets of medication produced an hour, and it all starts at the front of the line where raw ingredients are carefully mixed, measured and monitored in large stainless-steel tanks.
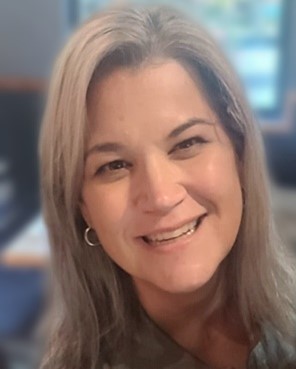
It’s a finely tuned process; but what happens if something goes wrong with the pressure in these stainless steel tanks, for example? Plant workers depend on notifications for even the slightest pressure change, which could mean the difference between a smooth running, meticulously calculated production line and a major catastrophe.
Alarming Scenarios
It’s an alarming scenario that threatens plants daily. The ability to monitor critical process variables and be notified when something is not right is vitally important in every stage of industrial manufacturing and utility processes.
But how do you ensure those notifications are seamlessly transferred to your operations and automation teams, and even beyond to business offices or whomever needs to know?
It’s something we’ve been talking about for years and is now becoming commonplace in language, but is it in practice?
Digital Transformation. IIoT. Industry 4.0. While they may seem like just trending buzz words, the technologies are critical to your operation being efficient and competitive, while reducing unplanned downtime.
Alarm #1 – End Users: Where to Start
Those of us in the system integration industry are well-aware of the engineering concepts and practices that bring these terms to life.
In reality, business owners and C-level executives who hold the financial keys to make this a possibility often do not. Their focus typically is on the big picture, so it’s important to help them understand how and why this technology affects day-to-day business operations.
First, we have to define it for them, not in highly technical terms, but in conceptual understanding.
Digital transformation is exactly what it sounds like; the entirety and ongoing process of transforming business operations and products with digital solutions. Moving away from the manual processes that are more labor intensive and preparing companies to get ready for the future and what’s coming next.
The Industrial Internet of Things (IIoT) refers to data and the collection of data, everything from sensors and computer applications to the manufacturing processes and energy movement.
When both digital transformation (the process) and IIoT (the data collection) are merged to deliver real-time data and analytics that positively impact your business decisions, you’re showcasing what Industry 4.0 is all about. Then we, as system integrators (SI), have to be able to bring data to life for our customers so they can see the ROI of digital transformation.
Alarm #2 – Supply Chain Issues Wreaking Havoc
The combination of supply chain issues caused by the 2020 pandemic and the costs of upgrading technology sets an alarming stage. Unfortunately, there is not a magic cure to solving supply chain issues and though we are starting to see signs that the burdens will lift, we are not there yet.
Right now, we know that analog I/O modules have long lead times and, since that’s a fundamental piece of the digital transformation process, it can be difficult to move forward.
But with careful planning and dedicated time spent in the design phase of a project, engineers can find creative and alternative solutions to analog modules.
Consider ethernet-enabled devices instead of analog or systems like DeviceLink that may operate in a similar manner using different technology.
This is where the expertise of a trusted partner comes in.
Navigating alternative solutions requires a breadth of knowledge that not all integrators have. But forward-thinking SIs regularly look for alternative ways to keep their customers moving ahead using the latest technologies.
Alarm #3 – Navigating the IT/OT Divide
This alarm might be the biggest one yet, bridging the gap between IT and OT. We see this often in our projects. Both the IT specialist and automation teams on the OT side have important jobs, and critical compliance and security measures to follow. They are all well-meaning.
But a lack of communication about the right issues can cause significant disruptions to business and production systems that can be costly and frustrating.
An SI really understands both sides of the equation and, more importantly, is often an objective outsider who can step into the middle of a conversation to ask the right questions up front and avert major headaches down the line.
Often, because professionals on both sides of the IT/OT spectrum are so specialized in their area, they may not even be aware of all the questions that need to be asked.
That’s where a skilled SI can step in because they will know first, the questions that need answered and second, how to navigate a solution so both sides are equally protected in the end and fully, efficiently productive.
Yes, there are alarming truths about digital transformation that still need to be solved and realities that present future opportunities. However, just because an industry starts talking about a trending term or new concept doesn’t mean it will be fully ready to adopt it.
That said, companies that position themselves for a competitive future in the marketplace fully embrace the digital transformation journey and all that it entails. Helping with this journey are companies with whom you can seamlessly partner to provide solutions that notify you in every way possible about equipment problems: via mobile app, text, voice, email, or in-plant announcements, which means problems get fixed faster, waste is reduced, and maintenance and staff costs go down.
It all comes down to trust. Who do you trust to design and monitor your most valuable processes when everything is on the line – safety, security, productivity, and efficiency?
Who will you call to get the job done right?
It’s important to foster and build these relationships so trust is foundational in every project you take on as you journey through digital transformation.
Keith Mandachit, PE, is the Engineering Manager, Huffman Engineering, Inc., and can be reached at kmandachit@huffmaneng.com.
Barbara Padgett is the Marketing Manager, WIN-911, and can be reached at barbara.padgett@win911.com.
This content is sponsored by WIN-911.